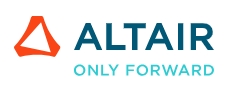
澳汰爾工程軟件(上海)有限公司
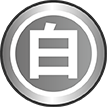
已認(rèn)證
澳汰爾工程軟件(上海)有限公司
已認(rèn)證
感謝成都航天模塑有限責(zé)任公司孫正峰投稿
工裝設(shè)計在制造前,需具備一定的剛強(qiáng)度指標(biāo),以滿足結(jié)構(gòu)功能試驗。采用傳統(tǒng)的有限元仿真分析,雖然精度可以保證,但是時間較長,且需具備一定的專業(yè)能力。為了提高效率,可以采用 SimSolid 無網(wǎng)格進(jìn)行仿真分析。
本文采用有限元仿真和 SimSolid 無網(wǎng)格對比分析,最后和試驗進(jìn)行對標(biāo)。
一、背景
隨著產(chǎn)品結(jié)構(gòu)力學(xué)性能測試的急劇增加,要求越來越嚴(yán)格,應(yīng)用場景也在不斷更新。為了能滿足測試需求,針對不同測試要求需要設(shè)計不同配置的工裝,久而久之,工裝越來越多,成本也越來越高,且安裝操作也較繁瑣。面對有些大載荷工況(載荷≥2500N),公司配備的試驗設(shè)備無法滿足,只能委托其他試驗機(jī)構(gòu)進(jìn)行測試,這樣一來,試驗成本、工裝成本、人力成本等也隨之增加。
基于上述現(xiàn)狀,公司開發(fā)設(shè)計了一款大型通用工裝,結(jié)合公司新配置的設(shè)備,針對不同測試要求可選擇性搭配,且可滿足不同位置、不同角度、不同載荷大?。ㄝd荷最大可達(dá)10000N)的功能性測試。
測試工裝設(shè)計好后,在制造之前,需要驗證其剛強(qiáng)度性能,這類復(fù)雜工裝的有限元仿真驗證,要求仿真人員具備較專業(yè)的網(wǎng)格模型搭建能力,并且存在仿真時間長迭代慢的問題,所以探索了無網(wǎng)格快速仿真軟件,測試無網(wǎng)格結(jié)構(gòu)仿真的精度和效率。
二、數(shù)據(jù)模型
大型通用工裝尺寸為2410mm×1710mm×1800mm,總重628kg,采用鋁合金和鈑金相結(jié)合的方式,如圖1所示:
圖1 大型通用工裝數(shù)據(jù)模型圖
如圖1所示,灰色部件為鋁合金材料,其余部件均為鈑金材料。
三、有限元仿真分析
3.1 網(wǎng)格劃分及連接方式
工裝總共由183個零部件組成。鋁合金及大部分鈑金均采用殼單元,即中面四邊形網(wǎng)格,網(wǎng)格尺寸大小為4mm,不同截面分別賦予不同料厚,如圖2所示;剩余部分鈑金件采用六面體網(wǎng)格,為了保留產(chǎn)品的所有特征,網(wǎng)格大小采用2mm,如圖3所示。鋁合金件之間通過角碼進(jìn)行連接,鈑金件之間通過焊接及螺栓進(jìn)行連接??偝删W(wǎng)格及連接如圖4所示。網(wǎng)格單元總數(shù)量為1645393個。
圖2 中面四邊形網(wǎng)格
圖3 六面體網(wǎng)格
圖4 有限元網(wǎng)格總成裝配圖
3.2 材料參數(shù)
鋁合金和鈑金材料參數(shù)如表1所示。
表1 大型通用工裝材料參數(shù)
3.3 分析工況
為了驗證工裝的可靠性,需要保證工裝具有一定的剛性,同時,在大載荷作用下,工裝具備足夠的強(qiáng)度。因此,對工裝采用剛度和強(qiáng)度的結(jié)構(gòu)力學(xué)分析。
約束:對工裝底部4個腳進(jìn)行全約束,即約束dof1~dof6。
載荷:對工裝與產(chǎn)品的連接點進(jìn)行加載,剛度載荷大小為1000N,測量點位上橫梁中間位置,目標(biāo)值為≤0.5mm;強(qiáng)度載荷大小為5000N,最大應(yīng)力<材料屈服強(qiáng)度×0.8。
工裝仿真分析工況如圖5所示:
圖5 工裝仿真分析工況示意圖
3.4 仿真分析結(jié)果
工裝剛度仿真分析結(jié)果如圖6所示:
圖6 工裝剛度仿真分析位移云圖
由圖6所示,工裝剛度工況,指定點位移為0.104mm。
工裝強(qiáng)度仿真分析結(jié)果如圖7所示:
圖7 工裝強(qiáng)度仿真分析應(yīng)力云圖
由圖7所示,工裝強(qiáng)度工況,最大應(yīng)力為45.8MPa,低于材料屈服強(qiáng)度的0.8倍。
小結(jié):有限元仿真分析網(wǎng)格劃分、連接、分析設(shè)置等,總共耗時7天時間(平均每天按照7個小時計算)。
備注:此有限元仿真分析為工作一年工程師的效率。
四、SimSolid仿真分析
鑒于有限元仿真分析耗時耗力,因此考慮 SimSolid 無網(wǎng)格軟件。首先導(dǎo)入幾何模型,如圖8所示:
圖8 導(dǎo)入幾何模型
導(dǎo)入幾何模型后,對總成數(shù)據(jù)進(jìn)行自動綁定接觸,間隙和穿透均設(shè)置為0.5mm,設(shè)置如圖9所示:
圖9 自動綁定接觸設(shè)置
接著進(jìn)行約束和載荷工況設(shè)置,如圖10所示:
圖10 約束和載荷工況設(shè)置
分析設(shè)置和分析方法均和有限元仿真保持一致,即采用線性靜力學(xué)分析,如圖11所示:
圖11 線性靜力學(xué)分析
求解設(shè)置采用Adapt for stiffness進(jìn)行,如圖12所示:
圖12 求解設(shè)置Adapt for stiffness
分析結(jié)果如圖13所示:
圖13 基于求解設(shè)置Adapt for stiffness的位移云圖
由圖13可知,提取與有限元仿真位移云圖中相同的點,指定點位移為0.075mm。
此結(jié)果與有限元仿真位移云圖中相同點位移結(jié)果0.104mm相差較大,誤差達(dá)到27.9%。結(jié)合模型進(jìn)行誤差原因分析:由于幾何模型厚度較薄,且長度較長,符合薄壁件特征,因此,將求解設(shè)置改為Custom,同時勾選 Adapt to features 和 Adapt to thin solids,Refinement level 選擇higt,如圖14所示:
圖14 求解設(shè)置Custom
根據(jù)求解設(shè)置Custom,其分析結(jié)果如圖15所示(SimSolid 的云圖和有限元的云圖對比):
圖15 基于求解設(shè)置Custom的位移云圖
由圖15可知,提取與有限元仿真位移云圖中相同的點,指定點位移為0.094mm。
此結(jié)果與有限元仿真位移云圖中相同點位移結(jié)果0.104mm相差較小,誤差僅9.6%。
剛度誤差<10%可接受,按照同樣的分析方法,將載荷改為5000N,其應(yīng)力云圖如圖16所示(SimSolid的云圖和有限元的云圖對比):
圖16 基于SimSolid的強(qiáng)度分析結(jié)果-應(yīng)力云圖
由圖16所示,基于SimSolid的強(qiáng)度分析結(jié)果,最大應(yīng)力為42.3MPa。
此結(jié)果與有限元仿真應(yīng)力云圖中最大應(yīng)力結(jié)果45.8Mpa相差較小,誤差僅7.6%。
小結(jié):SimSolid 仿真分析綁定接觸、連接、分析設(shè)置等,總共耗時1.5h。
五、試驗結(jié)果
試驗工裝總成如圖17所示:
圖17 試驗工裝總成
試驗按照與有限元仿真加載點位置、大小和方向一致進(jìn)行,試驗測量點與仿真分析結(jié)果選取點一致,加載1000N載荷下的試驗結(jié)果如圖18所示:
圖18 試驗剛度結(jié)果
由圖18可知,試驗測量點(與仿真分析結(jié)果選取點一致)位移為0.139mm。相比有限元仿真分析結(jié)果0.104mm和 SimSolid 分析結(jié)果0.094mm大一些。
誤差原因分析:從圖17可以看出,工裝底部放置在地面上,僅地面對工裝有支撐作用,試驗過程中,工裝受力后,會有一點翻轉(zhuǎn)的趨勢,仿真中四個底角是全約束,沒有考慮結(jié)構(gòu)翻轉(zhuǎn)。因此,造成試驗結(jié)果比有限元分析結(jié)果和 SimSolid 結(jié)果都偏大,屬于正常范圍。
接著對工裝進(jìn)行5000N強(qiáng)度試驗,由于沒有應(yīng)變片,因此,無法檢測應(yīng)力,只能通過實驗結(jié)果觀察工裝有無永久變形和發(fā)白的現(xiàn)象,如圖19所示:
圖19 工裝強(qiáng)度5000N試驗結(jié)果圖片
由圖19可知,工裝強(qiáng)度5000N試驗卸載后,沒有永久變形。
六、對標(biāo)
將 SimSolid 結(jié)果、有限元仿真結(jié)果、試驗結(jié)果進(jìn)行對標(biāo),如表2所示:
表2 SimSolid結(jié)果、有限元仿真結(jié)果、試驗結(jié)果對標(biāo)
備注:
1.試驗結(jié)果與仿真結(jié)果分析:工裝底部放置在地面上,僅地面對工裝有支撐作用,試驗過程中,工裝受力后,會有一點翻轉(zhuǎn)的趨勢。仿真中四個底角是全約束,沒有考慮結(jié)構(gòu)翻轉(zhuǎn)。因此,造成試驗結(jié)果比有限元分析結(jié)果和 SimSolid 結(jié)果都偏大,屬于正常范圍。后續(xù)減小仿真與試驗差異的操作是,更改仿真時底角的約束,使其更貼近試驗條件。
2.SimSolid 與有限元仿真對比,SimSolid 與有限元仿真的位移差異為-0.01mm,體現(xiàn)在百分比上是9.6%,應(yīng)力差異是-3.5MPa,體現(xiàn)在百分比上是7.6%。該精度已能指導(dǎo)設(shè)計,且提速明顯。
3.SimSolid 與有限元仿真,差異來源可能是有限元模型中部分殼單元的簡化偏離了原始模型,使得在局部幾何上有限元模型與 SimSolid 模型不一致。
七、總結(jié)
針對大型復(fù)雜的工裝,零件數(shù)量又龐大的類型,前處理模型搭建(即殼單元和六面體網(wǎng)格劃分、單元連接等)非常費(fèi)時間,且搭建的模型網(wǎng)格數(shù)量也多,計算時間也較長,采用 SimSolid 無網(wǎng)格進(jìn)行仿真分析,不僅能大大縮短時間,同時能保證精度,具體結(jié)論如下:
1.SimSolid從導(dǎo)入模型到結(jié)果查看,總計耗時1.5h,而有限元仿真分析導(dǎo)入模型到結(jié)果查看,總共耗時49h,僅有限元仿真總時長的3%。(備注:此有限元仿真分析為工作一年工程師的效率。)
2.SimSolid 與有限元仿真,剛度和強(qiáng)度誤差可控制在10%以內(nèi)。
3.針對薄壁零件,采用 SimSolid 進(jìn)行仿真分析時,建議將求解設(shè)置改為 Custom,同時勾選Adapt to features和Adapt to thin solids,Refinement level 選擇 higt,這樣可以提高仿真精度。
4.SimSolid、有限元仿真、試驗結(jié)果基本一致,可以滿足試驗要求。
八、展望
1.目前我用的這個2020版本無法創(chuàng)建質(zhì)量點,無法創(chuàng)建剛性單元等,最新的2025版本可以支持等效創(chuàng)建剛性單元、創(chuàng)建質(zhì)量點,新增的建模功能可更好對標(biāo)有限元模型,降低精度差異,因此,后續(xù)我也會下載最新版本進(jìn)行對標(biāo)分析。
2.目前 SimSolid 無網(wǎng)格仿真方法是有限元隱式算法類似的外部近似方法,無法仿真碰撞,期待后續(xù)能有沖擊碰撞類顯式問題的快速仿真。
2025年5月15日,來自全球不同行業(yè)的知名企業(yè)專家將線上實時分享他們使用快速仿真設(shè)計的實戰(zhàn)經(jīng)驗,歡迎您報名會議,了解如何利用仿真技術(shù)加快產(chǎn)品研發(fā)速度, CAE 和有限元分析技術(shù)的應(yīng)用如何在產(chǎn)品研發(fā)中實現(xiàn)降本增效。
關(guān)于 Altair 澳汰爾
Altair 是計算智能領(lǐng)域的全球領(lǐng)導(dǎo)者之一,在仿真、高性能計算 (HPC) 和人工智能等領(lǐng)域提供軟件和云解決方案。Altair 能使跨越廣泛行業(yè)的企業(yè)們在連接的世界中更高效地競爭,并創(chuàng)造更可持續(xù)的未來。
公司總部位于美國密歇根州,服務(wù)于16000多家全球企業(yè),應(yīng)用行業(yè)包括汽車、消費(fèi)電子、航空航天、能源、機(jī)車車輛、造船、國防軍工、金融、零售等。
最新動態(tài)
更多
虛擬號將在 秒后失效
使用微信掃碼撥號